1.粉末の組成
目的を達成するための組成を選定し、それらの皮膜が容易に形成できれば問題ないのですが、多くの場合、簡単ではありません。
卑近な例では、耐摩耗性皮膜として多くの実施例のあるWC-Coがあります。本来、硬度から見ればWCのみでも良いのですが、これだけでは皮膜形成が非常に困難であり、皮膜形成できたとしても非常脆く、使用に耐えないものとなります。そこで、皮膜の形成と皮膜の靱性向上のためCoの添加が必要になるわけです。これは、超硬合金と称され、切断、切削用工具に使用されている焼結合金と同様の理由ですが、溶射の場合は、それらより、さらに多くのCoが必要です。
この例からわかるように、目的を達成するための成分だけでなく、たいていの場合皮膜形成のため、さらに形成された皮膜が使用に耐える強度、靱性を維持するための成分も考慮する必要があります
2.粉末の形態及び製造方法
溶射用粉末の代表的な製造方法には次のようなものがあります。
1) アトマイズ(ガス、水)
2) 粉砕(溶融粉砕、焼結粉砕)
3) 造粒(スプレー造粒、練り込み造粒、流動層造粒等)
4) 被覆(めっき、コーティング)
5) その他(加圧水素還元法、メンストラム法等)
これらの製法で作られた粉末のSEM写真を図1、図2に示します
a) b)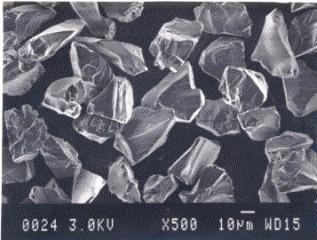
c) d)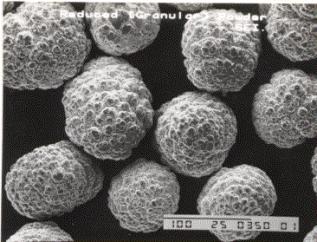
図1 単相粉体
a) CoNiCrAlY 製造法 ガスアトマイズ
b) Al2O3 製造法 溶融粉砕
c) Mo 製造法 スプレー造粒
d) Ni 製造法 加圧水素還元
a) b)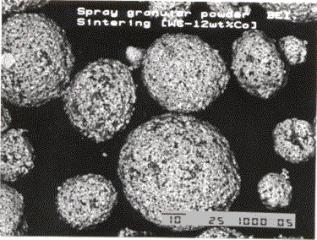
c)
図2 複合粉体
a) WC-12mass%Co 製造法 溶融粉砕
b) WC-12mass%Co 製造法 造粒焼結
c) Graphite-75mass%Cu 製造法 無電解めっき
これらの写真を見ると解るように、製造方法により、それぞれ特徴的な形態を示します。当然、組成は同じでも、形成される皮膜特性は異なります。
現状、製造コスト及び製造装置の完成度等の兼ね合いもあって、溶射用粉末のほとんどは1)〜3)のい ずれかの方法で製造されています。
それぞれの特徴を表1に示します。
以上の、特性を考慮し、目的に適合する粉末の形態、製造方法を選択しなければなりません。
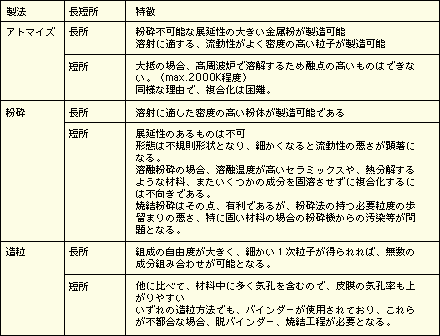
表1.製造方法の特徴
3.粒度
一般の粉末と比較して、溶射用粉末の特徴は下限を有する点です。例えば、焼結用粉末では上限を 決めます(例えば75μm全量通過)が、溶射粉末は上限だけでなく下限も必要(例えば上限45μm、 下限10μm)となります。これは、粉末供給機から溶射ガンまで、細いチューブを通して搬送するので、 良好な流動性が必要なためと、溶射ガンから基材まで飛行して皮膜を形成するには、ある程度の慣性 が必要なためです。
最終的な粉末の粒度は、材料の熱的性質、使用する溶射装置によって決定されます。定性的には次 のようになります。
1) 溶融の容易さ
容易なほど粗いものが使用されます。
2)変形の容易さ
容易なほど粗いものが使用されます。
3)ガンの特性
そのガンの熱源の温度と粉末への与熱量で決まり、その能力が高いほど粗いものが使用できます。ただ し、下限はそのガンの機械的要因(細かいとノズルが詰まる、粉末が供給できない等)で決まる場合もあ ります。
さらに、造粒法においては1次粒子の選定が重要となり、それによる皮膜特性も異なってきます。例として、図3に通常使用されているWC-12mass%Co造粒焼結粉末のWC1次粒子と造粒体の粒度を変化させ たものを示します。
この粉末においては、一般的にWC粒子を大きくするほど、皮膜は緻密になり、歩留ま りは低下します。
造粒体粒度は上述の条件に加えて、使用する溶射機によっても、決定されます。れは機器によりガン構 造や出力が異なるので、ガン内およびその出口での閉塞や付着状況が異なるためです。一般的に、出 力が高いほど、また粉末がガン内部に供給されるものは粗いものが適用されます。その代表的な粒度は おおよそ次のようなものです。
一般の外部供給型プラズマ溶射機 -45+10μm
小容量HVOF(内部供給型) -32+5μm
大容量HVOF(内部供給型) -53+15μm
a) b)
c)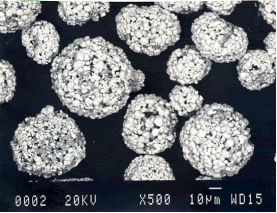
図3 1次粒子及び2次粒子の異なるWC-12mass%Co粉体
a)1次粒子:1μm 2次粒子:-53+15μm
b)1次粒子:3μm 2次粒子:-32+5μm
c)1次粒子:6μm 2次粒子:-53+15μm
|